一、研究的背景与问题
由于异形坯断面形状不规则,受力情况复杂,在连铸生产中容易出现裂纹、夹渣等缺陷,导致轧制时产品报废率高。国内的几台大断面异形坯铸机均为国外引进,其最大断面为1024mm×390mm×120mm。而国产的两台异形坯铸机生产的异形坯最大宽度只有500mm,和引进铸机还存在较大的差距,我国此前还没有完全掌握异形坯铸机核心技术。当需要生产新的断面时,只能简单仿制,往往使用效果较差,铸坯质量难以保证。随着,我国的基础建设不断投入,我们需要大量产线更丰富的异形坯铸机,而且还需要进一步加大其断面。为此,开发我国用于轧制重型H型钢的重型异形坯连铸机技术与装备非常重要。
重型异形坯断面尺寸更大,铸坯的凝固进程更长,应力情况非常复杂。铸坯对整个凝固过程的传热均匀性,以及设备的刚度提出了更高的要求。同时兼顾板坯、非对称异形坯的生产,对夹持段也有一些特殊的要求。冶金控制模型应稳定、可靠,确保铸坯的坯壳均匀生长,表面温度平稳下降。设备结构合理,以保证较高对弧精度,同时更换快捷。
从设备设计、模型开发两方面着手,开发的设备结构为计算模型提供基础,模型计算结果为设备开发提供理论依据,相互验证、推动。在形成一套完整的重型异形坯铸机装备的同时,给出详实可靠的理论支撑。研发出的冶金模型,辅助设备设计的同时,得到合理的连铸工艺,形成一整套生产工艺参数。使研发的设备、工艺参数做到有的放矢,确保铸机投产后稳定生产。
重型异形坯的关键设备中,结晶器的冷却非常重要,要充分考虑到初生坯壳各个角部的二维冷却,以及不同部位的支撑方式。异形坯二次冷却区的辊列支撑、喷嘴布置,要满足铸坯生长过程的冷却、支撑作用。采用离线仿真模型,对凝固过程进行模拟,优化设计,避免热应力、鼓肚应力引起的裂纹。采用二冷水动态控制,保证铸坯表面温度按目标设定值平稳下降。中包控流、水口设置、引锭头设计、开浇水量的控制都有严格的要求,需要完整的工艺参数。以上都是本项目需要研究解决的关键问题。
二、解决问题的思路与技术方案
总体研发思路为,从设备开发、模型开发两方面着手,通过设备研发为计算模型提供基础,模型研发为设备开发提供理论依据,相互验证、推动。在形成一套完整的重型异形坯铸机设备的同时,提出详细的理论支撑。开发出相应的冶金模型,辅助设备设计的同时,得到合理的连铸工艺,形成一整套生产工艺参数。使研发的设备、工艺参数做到有的放矢,确保铸机的稳定生产。
1、文献调研。收集目前国内外关于异形坯铸机的相关文献、专利以及应用情况,确定当前技术的优缺点;分析重型异形坯铸机的关键参数,确定要重点解决的环节,制定合理的方案路线;
2、铸机机型的确定,对重型异形坯铸机的核心设备:结晶器、夹持段、拉矫系统,进行系统开发。确保异形坯、板坯生产的兼容性,根据异形坯、板坯兼容生产,确定板坯扇形段的结构,辊子的特殊冷却方式;
3、通过对结晶器内铸坯传热过程进行模拟计算,确定结晶器冷却结构、锥度、开口度等关键参数;
4、开发异形坯凝固过程仿真模型,对喷嘴、二冷、辊列辅助设计系统开发。冷却区和喷嘴为空间布置,其喷出的水量最终转化为铸坯表面的水流密度。再通过传热计算,得到不同铸坯表面温度,对冷却回路、喷嘴布置进行优化。通过对二冷区的铸坯鼓肚状态的模拟分析,对夹持段的辊列进行校核;
5、二冷动态控制模型开发,异形坯的二冷水控制,采用基于“坯龄模型”二次冷却动态控制。由于有效拉速考虑到了铸坯坯壳的生长情况,考虑到了铸坯的传热和凝固特点,进行动态冷却控制,使铸坯按目标表面温度曲线缓慢下降。为了提高计算速度,实现多流并行计算,采用“间断伽略金有限元”算法编写异形坯温度场在线计算程序。用于实时计算连铸坯的温度场,进行在线热状态监测。可以直观地显示浇铸过程中铸坯表面特定位置的冷却曲线和凝固热节点处的固相率曲线,揭示铸坯冷却的均匀状态。
三、主要创新性成果
1、针对重型异形坯连铸机的装备空缺和设计难点,对核心关键装备技术方面开展了研究,实现了重型异形坯铸机的完全国产化,不仅填补了我国重型异形坯铸机的技术空白,而且创造了多项国际领先技术指标。生产的重型异形坯尺寸(1200mm×500mm×120mm)为国际上已投产同类异形坯最大规格。
(1)【难题】重型异形坯结晶器的宽面形状复杂,采用铜板上打孔的冷却结构,如图1所示。异形坯结晶器几个角部区域的传热控制是铜板设计的关键,通过优化开孔的大小、间距,尽量提高传热的均匀性。重型异形坯结晶器重量较重,而且异形坯的摩擦力也较大,在仿弧过程中,意外载荷也要大于常规铸机。振动装置必须有足够的刚度,否则就会发生偏摆、共振等现象。【创新与成效】本研究从热量传导、应力分布的角度,搞清楚铸坯在结晶器内的凝固规律。通过建立二维传热-应力耦合模型,应用ANSYS有限元软件进行稳态热传导有限元分析,计算异形坯组合式结晶器铜板的弯月面区结晶器温度场,其温度分布如图2所示。通过模拟不同工况、开孔方式,将铜板热面的最大温差控制在60℃,大大减小铸坯局部的热应力。通过凝固过程的模拟,得到在结晶器内铸坯的收缩量,对结晶器的锥度进行合理设置,保证铸坯坯壳厚度的均匀增长。
通过对液压振动装置振动过程,进行模态分析和强度计算,如图3所示。分析其固有频率和应力分布情况,以实现对振动装置的结构进行优化,确保偏载情况下设备稳定性。
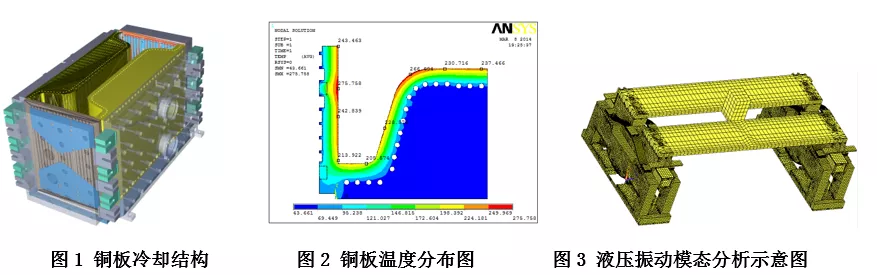
(2)【难题】铸坯进入夹持段后,坯壳很薄、铸坯温度较高。夹持段给铸坯支撑作用,防止铸坯的鼓肚,同时要进行喷水二次冷却,促使坯壳均匀生长。异形坯的形状较为复杂,如果设备夹持不合理,或二冷水冷却不均,机械应力、热应力就会导致铸坯表面、内部产生裂纹。重型异形坯的腹板较宽,最大的宽度达到了约900mm,腹板必须设置夹持辊直到全凝固。其翼板高度达到了500mm,而且翼板内侧是一个斜面,无法设置夹持辊,只能靠坯壳本身的刚度来支撑。当鼓肚变形发生后,在蠕变的作用下,其还有进一步加大的趋势。【创新与成效】异形坯夹持段复杂的结构、受力状况,需要建模计算其生产过程中的应力、应变情况,如图4所示。采用真实的铸坯几何形状,采用ANSYS三维实体模型进行模拟计算,计算该铸坯在生产过程中的鼓肚情况,作为夹持辊布置的设计依据。计算出的铸坯翼板、腹板鼓肚变形状况,如图5所示。生产表明,通过增加重型异形坯翼缘外侧的夹持辊,将外侧的鼓肚量控制在0.4mm以内,翼缘内侧的鼓肚量完全能够满足要求。

(3)【难题】异形坯的形状决定了其抗弯模量很大,不易矫直,如果矫直方式设置不合理,可能导致矫直后的铸坯翼缘发生变形,影响后工序的轧制。【创新与成效】矫直曲线、矫直力控制、驱动力的确定为拉矫系统的几个关键参数。本研究拉矫机的矫直曲线采用了连续矫直的方式,矫直过程中,铸坯的曲率是连续变化的,避免了矫直过程中的应力集中。对拉矫机各机架的驱动力分配进行计算,得到各机架的电机负荷系数,确定其电机、减速机的选型是否满足拉坯力的需要。通过模拟计算,得到不同工况下铸坯的变形、应力分布情况,以及拉矫机机架的应力分布情况,如图6所示,保证拉矫机长时间稳定工作。
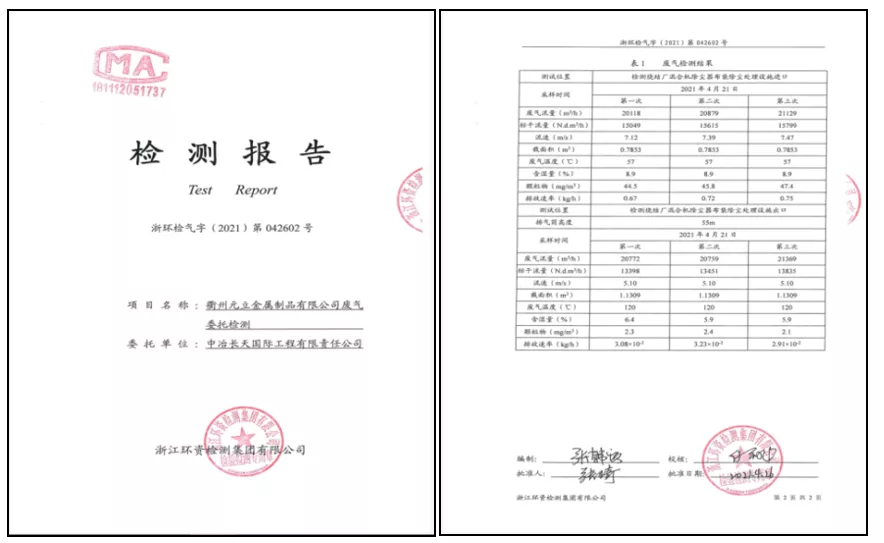
研发的国内首台重型异形坯连铸机,生产铸坯单重超过2t,最大宽度1200m,高度达500m,为世界最大断面异形坯。该铸坯通过万能型轧机轧制成大型云轨,用于高速云轨交通项目,如图7所示。

2、开发了重型异形坯连铸的核心工艺软件,包括异形坯凝固仿真模型,以及喷嘴、二冷、辊列的辅助设计系统等。
【难题】异形坯翼缘内侧带有一定的倾斜角度,拐角处的表面为曲面,断面上各点的散热条件差别很大,使得异形坯断面上各点的温差很大。二冷段喷嘴选型、辊列布置稍有不合理,会加剧这种铸坯表面温度的不均匀性,从而加大铸坯表面裂纹的倾向以及产生较大的鼓肚量。【创新与成效】本研究利用Gmsh三维有限元网格生成软件以及自编温度场计算程序,对二冷区铸坯的温度场进行计算,可以得到稳态下不同区域的铸坯横截面上的温度分布,以及各关键点的温降曲线,如图8所示。结合喷嘴、辊列辅助设计系统,确定出冷却区的划分、水量分布等参数,从而优化喷嘴和辊列的布置、选型。
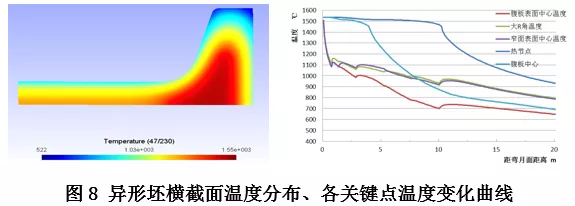
喷嘴、辊列辅助设计考虑了实际冷却区的布置,以及辊间喷嘴、辊子的空间分布,并根据实际的喷嘴布置计算铸坯表面的水流密度。以铸坯表面为计算区域,在横截面内,按照顺时针顺序划分网格,在拉坯方向按照等间距将网格进行拉伸得到整个计算区域。冷却区和喷嘴为空间布置,其喷出的水量最终转化为铸坯表面的水流密度。计算得到的水流密度分布、温度分布,异形坯各部位的鼓肚、应力分布情况,如图9所示。通过优化喷嘴的位置、流量、辊列布置,可以得到更加均匀的温度分布、鼓肚量,降低铸坯应力,减少裂纹的出现。

3、开发了异形坯二冷水在线动态控制系统,首次实现了异形坯的在线热跟踪。
【难题】异形坯因其几何形状复杂,无法采用正交、结构化的网格,用有限差分法进行计算存在困难,目前尚未见到异形坯连铸采用在线温度场计算的应用。因此难以实现二冷水的动态控制。【创新与成效】本研究开发了异形坯的二冷水动态控制模型,采用基于“坯龄模型”二次冷却动态控制,用等效拉速代替铸机的实时拉速,对铸坯进行二次冷却调节。根据在线温度场计算模型的计算结果,对二冷水动态调整,使铸坯按目标表面温度曲线缓慢下降。为了提高计算速度,实现多流并行计算,采用了“间断伽略金有限元”算法编写了异形坯温度场在线计算程序。用于实时计算连铸坯的温度场,进行在线热状态监测。可以直观地显示浇铸过程中铸坯表面特定位置的冷却曲线和凝固热节点处的固相率曲线,揭示铸坯冷却的均匀状态,如图10所示。在线温度场模型网格数:299万,计算时间:0.92秒,温度控制:±15℃以内。
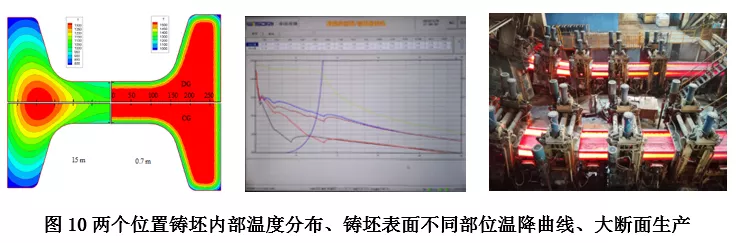
4、开发了非对称异形坯连铸技术,可显著提高云轨轧制效率、降低能耗,非对称异形坯为国际首创。
【难题】云轨和常规的热轧H型钢的不同之处,在于其上下翼缘的高度不同。不仅对轧钢工序、工艺提出了很多不同要求,而且对铸坯要求也不相同。采用常规的异形坯需要增加轧制道次,而且成材率不高。【创新与成效】开发一种非对称的异形坯,其上下翼缘高度根据轧钢需求而定。根据非对称异形坯尺寸的要求,开发出了相应的结晶器、夹持段设备,如图11所示。异形坯的鼓肚计算采用ANSYS实体模型计算,通过对比已有大断面异形坯的鼓肚变形情况,和非对称断面0.5m/min拉速时的鼓肚变形情况,确定密排夹持辊的分布,如图11所示。
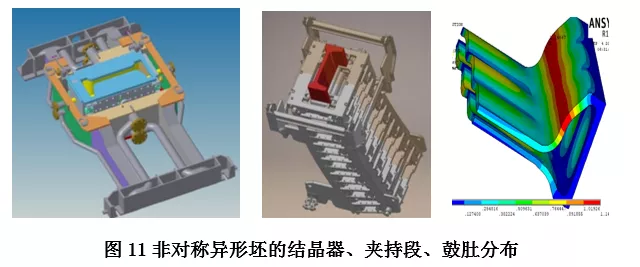
四、应用情况与效果
津西重型异形坯铸机投产后,迅速达产,和同类大型进口铸机相比,节约外汇~700万欧元,建设工期缩短一年。三年实现累计销售收入~55亿元,利润5亿元,为业主创造了巨大的经济效益。
本重型异形坯铸机技术的成功研发,满足了市场对大型H型钢坯料的需求,同时填补了国产重型异形坯铸机的技术空白。该铸机是我国第一套国产超大断面异形坯铸机,也是投产时世界上最大断面的异形坯铸机,标志着我国超大规格异形坯铸机的设计、制造、生产工艺达到世界领先水平,有力推动了大断面连铸技术的发展。为我国热轧重型H型钢的逐步推广使用,打下了坚实的基础,具备良好的社会效益。
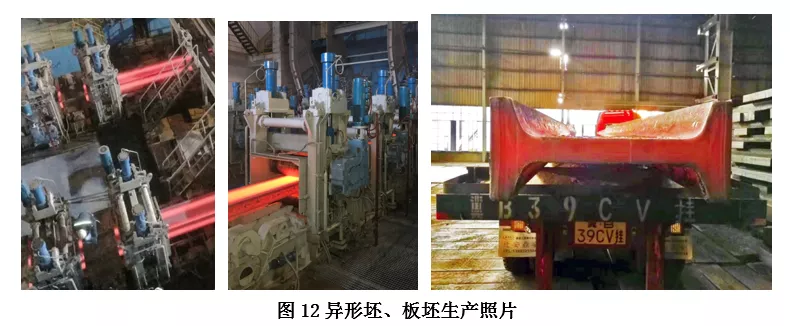
信息来源:中冶南方连铸技术工程有限责任公司